Senior Editor
- FMA
- The Fabricator
- FABTECH
- Canadian Metalworking
Categories
- Additive Manufacturing
- Aluminum Welding
- Arc Welding
- Assembly and Joining
- Automation and Robotics
- Bending and Forming
- Consumables
- Cutting and Weld Prep
- Electric Vehicles
- En Español
- Finishing
- Hydroforming
- Laser Cutting
- Laser Welding
- Machining
- Manufacturing Software
- Materials Handling
- Metals/Materials
- Oxyfuel Cutting
- Plasma Cutting
- Power Tools
- Punching and Other Holemaking
- Roll Forming
- Safety
- Sawing
- Shearing
- Shop Management
- Testing and Measuring
- Tube and Pipe Fabrication
- Tube and Pipe Production
- Waterjet Cutting
Industry Directory
Webcasts
Podcasts
FAB 40
Advertise
Subscribe
Account Login
Search
The quality benefits of quick response in metal fabrication
Michigan manufacturer Caster Concepts discovers the counterintuitive nature of quality control
- By Tim Heston
- March 16, 2024
- Article
- Shop Management
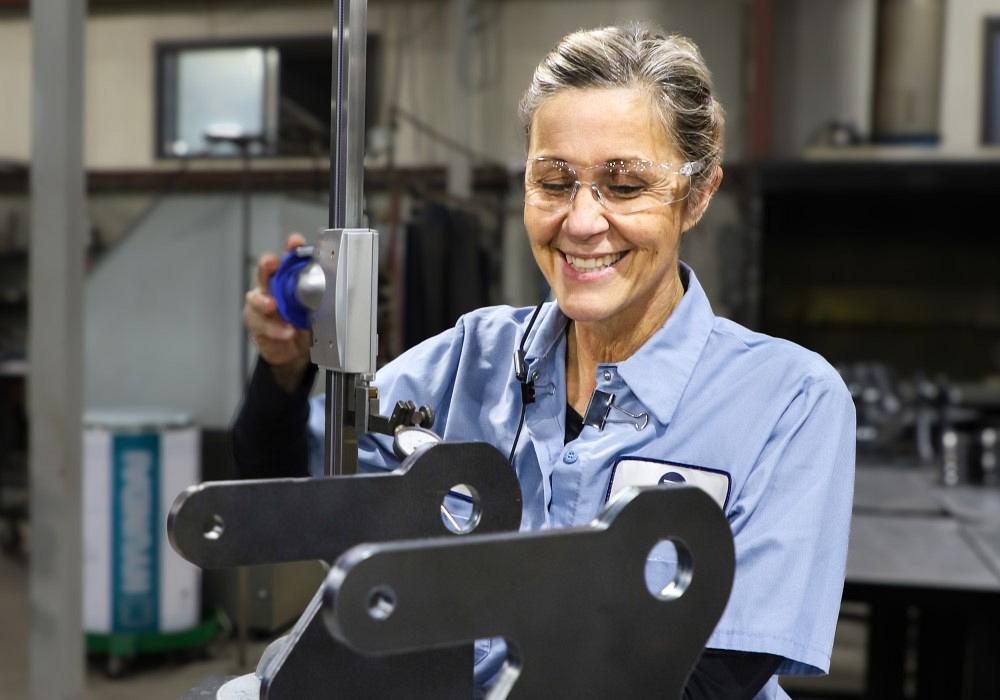
Jackie Willis, QC technician, performs in-process inspection adjacent to the fabrication cell. Images: Caster Concepts
Good quality control (QC) can be central to a fabricator’s success. If jobs don’t meet specs or the demands of downstream operations and the final customer, rework—the costliest form of waste—can skyrocket. QC is supposed to help prevent that.
QC also is a bit counterintuitive: Job-flow velocity matters. Caster Concepts, an Albion, Mich., manufacturer of heavy-duty casters and automated material handling equipment, noticed this immediately when it underwent a significant manufacturing transformation more than two decades ago. As it turns out, the better parts flowed, the easier and more effective QC got.
Enter QRM
Back in the early 2000s, Caster Concepts was searching for ways to streamline its process and improve its lead times and on-time delivery. As a company that delivers specialized products for a range of industries, product mix was unpredictable and lot sizes were highly variable. The company had reached out to some lean manufacturing consultants but didn’t have much success. Then, the production managers got into some reading that seemed to ring true for their high-product-mix operation.
The first was Eli Goldratt’s “The Goal,” the fictional narrative that describes the finer points behind the theory of constraints (manage flow by your bottleneck). The next was “It’s About Time” by Rajan Suri, professor emeritus at the University of Wisconsin-Madison and the founder of the Center for Quick Response Manufacturing, or QRM.
As Andrew Dobbins, vice president of manufacturing, recalled, “QRM really changed how we operate the manufacturing side of the business. We had manufacturing resources, but we weren’t applying them where they were needed. We had all this historical data, and we had thought the inventory we were making was the right inventory, that we were making the right products. That wasn’t always the case. We knew we had to find a more effective manufacturing process.”
The Hidden Wastes of Large Batches
QRM resembles lean manufacturing in some ways—excessive inventory isn’t good, for instance—but unlike lean, QRM is tailored for high-product-mix operations. A key metric is manufacturing critical-path time, or MCT. In “It’s About Time,” Suri defines MCT as “the typical amount of calendar time from when a customer creates an order, through the critical path, until the first piece is delivered to the customer.” In his books, Suri dives much deeper into MCT, which, in effect, sets the stage for the manufacturing transformation.
Like lean manufacturing, QRM recognizes that jobs spend most of their time sitting between operations. The actual time where work is being done and value is being added—the laser cuts, the brake bends, the welder welds—can be a matter of minutes or hours. But alas, it still takes weeks to deliver jobs to customers. For the most part, jobs sit on the floor in various traffic jams. Creating them is that build-to-stock, keep-the-machines-running mindset everywhere in the plant.
Imagine a brake operator bending a batch of parts and placing them on a pallet. Because of all the setup time, the shop groups like jobs together and fabricates ahead when it makes sense. Customers can simply pull from finished-goods inventory, and that inventory should provide a healthy buffer against those unexpected demand spikes. At least that’s how the thinking goes.
Right after bending, parts enter QC. QC personnel had signed off on the first article, but they found that something went awry later in the run. Nearly the entire batch had to be scrapped. That’s not the end of the world, the thinking went. Forming will just run the job again, and we’ve got that finished-goods inventory buffer there for a reason.
Of course, rerunning the job sends other jobs behind as well, and overtime ensues as rework mixes with rushed jobs. The increased chaos leads to more errors, rework, and unpredictability.
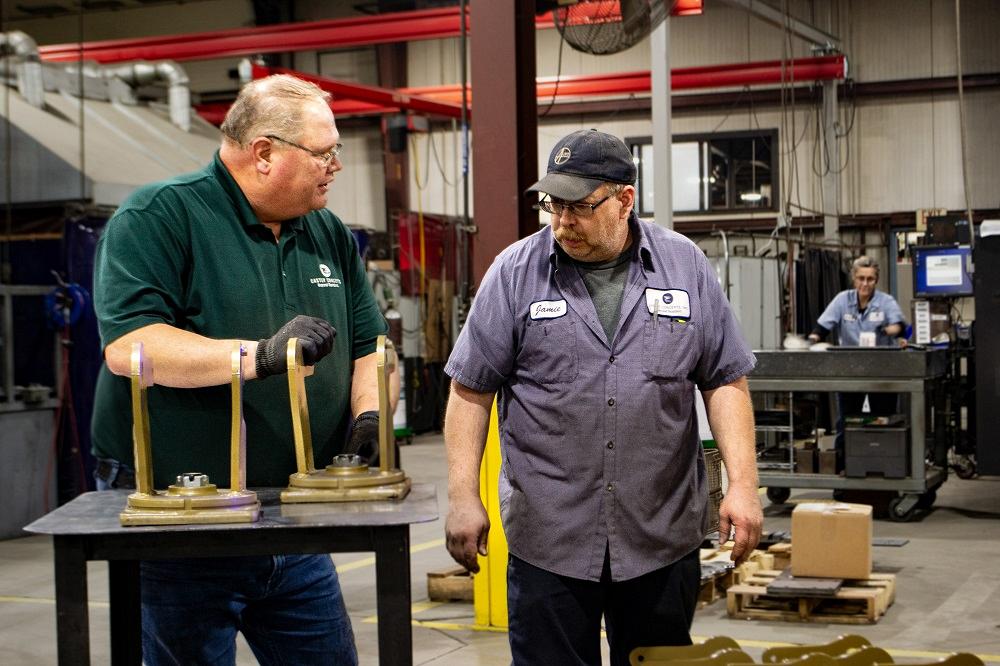
(From left) James Terry, scheduling manager, and Jamie Daglow, material handler, talk about the day’s production strategy. Continual communication helps catch problems early.
So, the shop doubles down. Managers obsess over machine uptime metrics. We need to produce so we have the inventory that customers need! Managers scrutinize past demand patterns and work with customers to develop better forecasts; production ramps up to feed finished-goods inventory. Laser-focused on machine utilization, supervisors strive to minimize setups whenever they can, grouping like jobs together. Of course, downstream workstations can’t do anything with all those large batches of work, so more work-in-process (WIP) inventory goes into racks.
WIP sits for weeks or even months before the bending department is ready for them—at which point, QC personnel checks the edges and discovers a problem that could have been caught months before.
Meanwhile, everyone’s workday has turned into a quixotic scramble, and company leaders soon realize that chasing windmills hasn’t helped the shop culture, customer relationships, or the bottom line.
Why Are You Making This?
The previous narrative is generic, not company-specific, but people at Caster Concepts, a 125-employee organization, remember similar experiences. Dobbins described an improperly machined caster arriving in assembly. It came from inventory, and the company already had more than 500 of those faulty parts in stock.
Dobbins recalled an epiphany he and others at the company had more than a decade ago. “There are certain moments in life you just remember. You never forget.”
It was during Bill Ritchie’s first visit. A now-retired QRM consultant, Ritchie walked by the multitude of racks full of WIP and finished goods. At the time, the company needed capacity for its growing caster business. He stopped, walked, turned, and asked, “Why are you making this stuff? Here’s your capacity, right here,” pointing to the rows and rows of inventory, unused, unsold, and aging. “You’ve got capacity. You just need to use it differently.”
QRM has many elements that can take some time to develop: separating the product mix into product families, organizing multiprocess manufacturing cells, amping up cross-training, transitioning away from the make-to-stock model, coordinating with suppliers and outside service providers. But one change can be done almost immediately, and it happened during Ritchie’s visit, just hours after he arrived.
“We’re a pretty flat organization. We don’t need to jump through hoops, and we can act quickly,” Dobbins said. “Almost immediately, we walked to the machining centers and fabrication equipment and started saying, ‘Stop the machine. We don’t need to run these parts anymore.’ QRM implementation began then and there.”
Flow in Fabrication
Now more than a decade later, QRM is still going strong. The company organized its work into multiprocess cells, where work flows from one manufacturing step to the next within minutes.
It implemented cross-training, too. Walk to the sheet metal and plate fabrication cell, and you’ll see the laser cutting operator move to forming and even welding. Everyone works as a team.
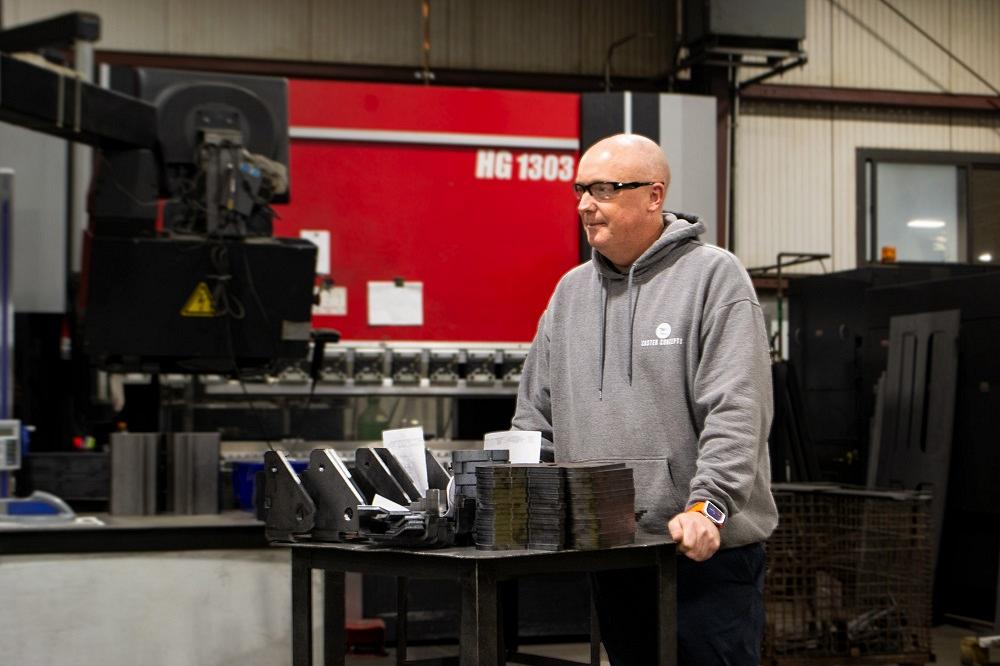
Andrew Dobbins, vice president of manufacturing, lends a hand moving cut and formed parts to the welding station nearby.
Cells are based around product families and related manufacturing processes. In fabrication, for instance, the AMADA fiber laser sits near the forming and welding stations. The cell produces all sheet metal and plate for the entire business. This includes caster components as well as formed sheets for a range of automated, heavy-duty material handling devices sold under the Conceptual Innovations brand. (Editor’s Note: Look out for further Conceptual Innovations coverage next month.)
When a laser cuts, it does so in small batches. Parts are denested and placed on carts that go directly to forming. If the brake is backed up, the laser simply stops cutting. Until the brake has capacity, there’s really no point in cutting more. That said, equipment still must perform reliably and be extremely flexible. Operators change over quickly, call up programs, and initiate forming within a few minutes.
No longer are machines scheduled to run at maximum capacity. Equipment utilization is important, as are quick changeovers. That said, the operation now is scheduled to run at no more than 80% capacity. Consider a highway at full capacity. Someone taps on the brakes, which causes the car behind to do the same, and the next car behind, and so forth. Within seconds, a minor brake tap snowballs into a major traffic jam. The same goes for a maxed-out shop floor. One minor, unexpected event can snowball into a major traffic jam. Run everything at 80% or less, more jobs get to their destination (the shipping dock) faster.
Overall, inventory is well below what it was in the early 2000s, but Dobbins described an important caveat: The goal isn’t to eliminate all inventory. The core function of inventory is to act as a buffer against variability. At Caster Concepts, cellular manufacturing and quick job flow has eliminated much of that variability; internal operations are no longer just feeding finished-goods inventory. Still, the company does hold some levels of inventory as a buffer against purchased items with long lead times. This includes forgings for casters. Despite the long lead times, those suppliers provide quality components the company needs.
“We’re also good customers of theirs,” Dobbins said. “We pay quickly. The success of our supply base is important to us,” adding that a strong supply base helps ensure on-time delivery to its customers.
Collaborative Quality
In the booklet, “MCT: Quick Reference Guide,” Suri writes, “A long MCT hides numerous quality problems throughout your enterprise and supply chain. Conversely, as MCT is reduced, quality issues are discovered quickly, root causes can be found, and improvements put in place.”
Watch Caster Concepts’ sheet metal cell in action, and you can see this happening—especially with QC. The company no longer has a central QC department. Instead, QC personnel are stationed at three mobile stations, each with a portable Keyence CMM. Operators use those stations to measure certain parts themselves. For complex work, QC personnel are called over to run the inspections.
This strategy, Dobbins said, exemplifies the company’s approach to cross-training. For certain work, operators are sufficiently qualified to inspect parts. For other parts, they call in the experts. That arrangement—plus the fact that laser, brake, and welding personnel work near each other—promotes conversation and discussion. They catch problems early, during or just after fabrication, not after a large batch has been sitting in inventory for months.
That, Dobbins said, might be the dominant reason behind Caster Concepts’ quality boost and, for that matter, its overall success with QRM. Employees no longer throw work over the metaphorical wall to the next manufacturing step, where a job becomes someone else’s problem.
Dobbins thought back again to that day he and the management team ordered most machines to stop producing parts to stock. Ironically, stopping everything didn’t put everyone behind. To the contrary, it unleashed capacity no one knew they had.
About the Author
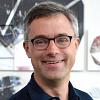
Tim Heston
2135 Point Blvd
Elgin, IL 60123
815-381-1314
Tim Heston, The Fabricator's senior editor, has covered the metal fabrication industry since 1998, starting his career at the American Welding Society's Welding Journal. Since then he has covered the full range of metal fabrication processes, from stamping, bending, and cutting to grinding and polishing. He joined The Fabricator's staff in October 2007.
Related Companies
subscribe now
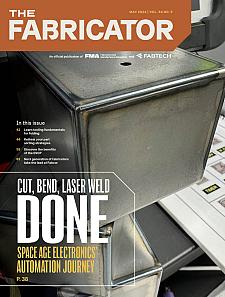
The Fabricator is North America's leading magazine for the metal forming and fabricating industry. The magazine delivers the news, technical articles, and case histories that enable fabricators to do their jobs more efficiently. The Fabricator has served the industry since 1970.
start your free subscription- Stay connected from anywhere
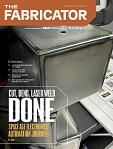
Easily access valuable industry resources now with full access to the digital edition of The Fabricator.
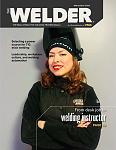
Easily access valuable industry resources now with full access to the digital edition of The Welder.
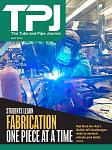
Easily access valuable industry resources now with full access to the digital edition of The Tube and Pipe Journal.
- Podcasting
- Podcast:
- The Fabricator Podcast
- Published:
- 04/16/2024
- Running Time:
- 63:29
In this episode of The Fabricator Podcast, Caleb Chamberlain, co-founder and CEO of OSH Cut, discusses his company’s...
- Industry Events
16th Annual Safety Conference
- April 30 - May 1, 2024
- Elgin,
Pipe and Tube Conference
- May 21 - 22, 2024
- Omaha, NE
World-Class Roll Forming Workshop
- June 5 - 6, 2024
- Louisville, KY
Advanced Laser Application Workshop
- June 25 - 27, 2024
- Novi, MI