Senior Editor
- FMA
- The Fabricator
- FABTECH
- Canadian Metalworking
Categories
- Additive Manufacturing
- Aluminum Welding
- Arc Welding
- Assembly and Joining
- Automation and Robotics
- Bending and Forming
- Consumables
- Cutting and Weld Prep
- Electric Vehicles
- En Español
- Finishing
- Hydroforming
- Laser Cutting
- Laser Welding
- Machining
- Manufacturing Software
- Materials Handling
- Metals/Materials
- Oxyfuel Cutting
- Plasma Cutting
- Power Tools
- Punching and Other Holemaking
- Roll Forming
- Safety
- Sawing
- Shearing
- Shop Management
- Testing and Measuring
- Tube and Pipe Fabrication
- Tube and Pipe Production
- Waterjet Cutting
Industry Directory
Webcasts
Podcasts
FAB 40
Advertise
Subscribe
Account Login
Search
La mezcla de gas auxiliar impulsa la tecnología del láser de fibra
La mezcla de nitrógeno y oxígeno le da un impulso al corte láser
- By Tim Heston
- April 8, 2024
- Article
- Laser Cutting
Apenas hace una década, la máquina de corte con láser de fibra era vista como una máquina especializada en chapa delgada. Los talleres pronto descubrieron que sólo tenían que invertir en una para competir, al menos para cortar su material de calibre. Para corte de placa de alta calidad, el láser de CO2 seguía siendo la opción a elegir. Por supuesto, los láseres de fibra podían cortar material más grueso, pero la calidad no era excelente, y al cortar placa muy gruesa, su ventaja de velocidad prácticamente desaparecía. Actualmente, ese mundo cambió.
Mejor gas, mejores cortes
La tecnología de gas auxiliar ha avanzado mucho en unos cuantos años, y es un gran contribuyente al constante cambio en el panorama del corte láser. El material de la lente y sus diseños han mejorado, así como las cabezas de corte y las boquillas. Un sistema moderno de alimentación de rayo láser de fibra puede ser visto usando inmensas cantidades de energía fotónica tranquilamente. Los láseres de potencia ultra-alta – 20, 30, hasta 50 kW – ahora están cortando placa gruesa de manera rápida e intachable.
“Intachablemente” es la palabra operativa aquí. El que el láser sea económicamente rentable se resume al costo por parte. Los láseres de alta potencia actualmente están avanzando en el ámbito del corte de placa de precisión. Si una parte solía cortarse con plasma y luego desbarbarse o acabarse en una fresadora, ahora podría hacerse por completo en el láser de fibra.
La mezcla de gas auxiliar ha ayudado a todo esto sea una realidad. Incluso las placas más gruesas actualmente se están procesando con una mezcla de nitrógeno-oxígeno, y no con sólo oxígeno. El chorro de gas auxiliar sigue siendo principalmente nitrógeno, un gas inerte que evacúa metal fundido de la rendija, pero un porcentaje pequeño de oxígeno (usualmente entre 1.5% y 5%) aporta la reacción química que ayuda a que el corte llegue hasta el fondo para un borde libre de escoria.
Las separaciones entre la superficie y la boquilla se han vuelto más pequeñas hasta ser casi inexistentes, todo en un esfuerzo por que ese flujo laminar de gas auxiliar fluya por la rendija, para que la mezcla de nitrógeno-oxígeno pueda funcionar como se espera. En el ámbito del corte de placa de precisión, una turbulencia excesiva del gas auxiliar es enemiga de un corte láser intachable.
Todo empezó con el aluminio
Las primeras aplicaciones de mezcla de gas surgieron hace más de una década – no para acero grueso, sino para corte de aluminio libre de escoria. Steve Albrecht, presidente de Liberty Systems, con sede en Hartland, Wisconsin, proveedor de mezclas de gas y generación de nitrógeno, recordó su trabajo con mezclas de nitrógeno-oxígeno a principios de la década de 2010, no para un láser de fibra sino para un sistema de CO2 de 4 kW que cortaba aluminio de 0.125 pulgadas de espesor.
“El aluminio tiene una capa superficial de óxido”, dijo Albrecht, “y se necesita atravesar esa capa para evitar escoria o rebabas”. Como lo descubrieron los ingenieros de aplicaciones, una corriente de gas auxiliar nitrógeno con cierta dosis de oxígeno ayudaba a eliminar esa escoria difícil de quitar en los bordes del aluminio cortados con láser.
“Siendo un material más suave, el aluminio tiene algunas características únicas para el corte láser”, dijo David Bell, presidente de Witt Gas Controls, Alpharetta, Georgia. “Y la mezcla de gas ayuda. Si usted corta aluminio con oxígeno, lo quema. Si lo corta con nitrógeno, se producen estriaciones en el borde. Si corta con una mezcla de ambos, obtendrá un corte mucho más intachable”.
La mezcla de gas evoluciona
Conforme los láseres de fibra empezaron a apoderarse del mercado, y las potencias disponibles siguieron creciendo, las estrategias del gas auxiliar evolucionaron. Los ingenieros de aplicaciones empezaron a experimentar con diferentes combinaciones de nitrógeno y oxígeno.
Como recordó Albrecht, cuando los ingenieros empezaron a tener buenos resultados con un contenido de oxígeno cercano al 20%, eso abrió la puerta para el corte con aire ultra-seco (y bien filtrado). Esto ofreció a los fabricantes ahorros significativos, especialmente considerando la cantidad de gas auxiliar que esos primeros láseres de fibra consumían.
“Cuando salieron los primeros láseres de fibra de 6 y 8 kW”, dijo Albrecht, “es ahí cuando el corte con aire ultra-seco realmente empezó a tomar vuelo”.
Sin embargo, conforme la potencia del láser de fibra siguió creciendo, las estrategias del gas auxiliar cambiaron. Las condiciones de corte para los láseres de fibra de la potencia más alta se han basado en mezclas precisas de nitrógeno-oxígeno, con cantidades menores de oxígeno (repito, una cantidad entre 1.5% y 5%, dependiendo de la aplicación y de la máquina).
Los OEMs (fabricantes de equipo original, por sus siglas en inglés) de máquinas de corte láser empezaron a experimentar con diferentes boquillas y diferentes maneras de lograr un flujo laminar uniforme de gas auxiliar en torno a un rayo cada vez más potente. Aumentaron los diámetros de boquilla. Algunos diseños de boquilla atrapan el gas arriba del metal; otras tecnologías usan “cortinas” de aire alrededor de la columna de gas auxiliar. Como lo explicó Albrecht, las estrategias dependen del fabricante de la máquina, pero todas tienen el mismo propósito: lograr la mejor calidad de corte al menor costo por parte. Esto incluye la utilización del gas auxiliar y, en particular, encontrar la mejor mezcla para mejorar tanto la calidad como la velocidad de corte.
Acerca del flujo
Aunque los OEM de máquinas han estado trabajando para optimizar el uso del gas auxiliar, los láseres de fibra de alta potencia que cortan material grueso a alta velocidad pueden seguir requiriendo mucho gas auxiliar. Un rayo de diámetro ancho que corta placa gruesa lo hace en medio de una gran columna de gas auxiliar que fluye por una boquilla con un orificio grande.
“Si corta más rápido, usa más gas”, dijo Bell. “Un láser solía usar 2,000 pies cúbicos (más de 56,000 litros) por hora. Actualmente están entre 4,500 y 5,000 pies cúbicos (entre unos 127,000 y 141,000 litros) por hora”.
Como explicó Bell, el corte láser exige varias demandas únicas de la mezcla de gas. Primero está una presión más alta. Un fabricante que, por decir, usa una mezcla de argón-CO2 para un gas de protección de soldadura, la presión probablemente no excederá 50 o 70 PSI. Siempre que la tubería alimente 125 PSI a la celda de trabajo, las demandas de presión pueden cumplirse.
“Para los láseres de fibra, la presión puede ser cuatro o cinco veces esa cantidad”, dijo Bell. Un mezclador para láser podría requerir 580 PSI en el sistema, simplemente porque la presión en el proceso de corte real puede ser hasta de 350 PSI. “Esto es algo totalmente diferente”.
Actualmente, un fabricante podría suministrar nitrógeno y oxígeno a un mezclador de diversas maneras. Podría usar nitrógeno líquido en gran volumen con cilindros o contenedores dewar individuales de oxígeno en cada láser; o podría tener un sistema de generación para el nitrógeno, cilindros para el oxígeno.
“En algunas aplicaciones, se puede usar sistemas de aire a alta presión para alimentar un mezclador junto con un suministro de nitrógeno puro, lo cual efectivamente eleva los niveles de pureza”, explicó Albrecht. “De esa manera, los fabricantes no necesitan tener cilindros de oxígeno tirados por ahí”.
Agregó que esta opción es particularmente popular para láseres entre 8 y 15 kW. “Ese sistema de aire podría cortar 80% del material, y el mezclador ayuda a mejorar la calidad al cortar acero suave más grueso, por ejemplo. Luego se podría usar nitrógeno líquido para acero inoxidable”.
Agregó que usar un suministro de aire para corte con gas mezclado actualmente no se está haciendo para 20 kW y potencias más altas. Ahora, la mayoría de los ingenieros de aplicaciones de los OEM de máquinas han estado trabajando para afinar las condiciones de corte con contenedores dewar o cilindros de oxígeno tradicionales. Repito, qué método funcione mejor depende de la aplicación y de las condiciones de corte del OEM del láser.
Acerca de la consistencia
La necesidad de una mezcla de gas consistente bajo condiciones altamente variables ha impulsado la tecnología hacia interfaces de control digital – no más válvulas de ajuste manual. Como lo describió Bell, algunos de los sistemas de mezcla más recientes de hecho son programables, lo que brinda la posibilidad de cambiar la mezcla de gas dependiendo del material que se esté cortando y de otras variables de la aplicación. Los tanques mezcladores son purgados de la mezcla antigua de gas antes de ser llenados con la nueva mezcla que se ajustó para el trabajo en turno. Además pueden comunicarse directamente con el láser. Cuando hay algo mal con el suministro de mezcla de gas, el láser lo sabe y puede apagarse antes de generar un mal corte.
“La industria ha avanzado mucho en pocos años”, dijo Bell. Ya no estamos en la mezcla 101 de gas”.
En cuanto al suministro de nitrógeno, los fabricantes tienen opciones tanto de nitrógeno líquido como de generación de nitrógeno. Independientemente de la configuración, nadie niega la importancia de la consistencia – en la calidad del gas así como en la presión y el flujo suficientes. Un mezclador tiene que ser capaz de satisfacer las demandas de las condiciones de corte cuidadosamente establecidas, diseñadas con base en cierta mezcla de gas, presión y flujo.
Para hacer esto, el oxígeno debe dispersarse uniformemente por la columna de nitrógeno en todo el programa de corte. Si el oxígeno se separa del nitrógeno, la calidad y el desempeño del corte pueden verse afectados. Diversas tecnologías de flujo y difusión intervienen para asegurar que el gas mezclado se mantenga uniformemente mezclado.
Un diseño de mezclador además necesita considerar los cambios en la demanda de presión y flujo del gas para cada láser. Cuando los parámetros de corte cambian – ya sea la velocidad de corte, el espesor del material o alguna otra cosa – esto demanda cantidades diferentes de gas auxiliar (es decir, diferentes presiones y volúmenes de flujo). Ese cambio en la demanda, dijo Bell, puede alterar la mezcla de gas. Lo que era, por decir, una mezcla de 95% nitrógeno/5% oxígeno repentinamente cambia a 90% nitrógeno y 10% oxígeno, lo cual puede ser una cantidad excesiva de oxígeno para los parámetros de corte diseñados para el trabajo en turno.
Todo cambio en la mezcla de gas necesita ocurrir de manera intencional y controlada, no sólo porque una máquina está extrayendo una cantidad diferente del sistema de mezcla de gas. Como lo explicó Bell, ésta es la razón de que muchos sistemas vengan con un tanque de compensación. Estos mezcladores de gas tipo receptor ayudan a mantener mezclas de gas específicas bajo las condiciones de flujo variantes – que se originan por cortar un nuevo espesor o por usar una nueva boquilla, por ejemplo.
Acerca de la tubería
Conforme los fabricantes se adentran en potencias láser más altas, la tubería del gas auxiliar se vuelve más crítica en general. Esto a su vez requiere una buena relación con un proveedor de gas que sepa la pureza del gas, el flujo y la presión que necesita un láser de fibra de alta potencia. Un mal trabajo de tubería que aporta contaminación (fundente de una conexión soldada que no se purgó correctamente, por ejemplo) puede causar estragos en la calidad del corte. Un buen proveedor de gas debe saber lo que se adapta mejor a la aplicación de un fabricante, incluyendo los requerimientos de pureza y de flujo.
Si un fabricante usa nitrógeno líquido, la búsqueda de un flujo consistente empieza en el tanque y en la tubería que va por el taller. Los talleres con varios láseres llevan el flujo de gas auxiliar nitrógeno de un tanque exterior grande hacia el taller – no en línea recta hacia los láseres, sino en un lazo. La mayor cantidad de tubería entre el tanque de nitrógeno y los láseres efectivamente hace una especie de tanque “de compensación”. Esto le da al sistema la reserva de nitrógeno que necesita cuando varios láseres de fibra de alta potencia empiezan a cortar al mismo tiempo.
“Si se tienen varios láseres y un tubo recto, generalmente al láser que está al final le faltará gas”, dijo Albrecht. “Por eso es importante tener lazos de tubo si hay varios láseres”.
Los tubos soldados pueden presentar problemas, pues existe el riesgo de que el fundente contamine el diámetro interior. Por esta razón, algunos sistemas de mezcla usan mangueras de Teflón trenzado reforzado y acoplamientos adecuados para evitar toda contaminación. Algunos sistemas de tanque de mezcla de gas de hecho se embarcan llenos de nitrógeno puro. Una vez instalados los tanques, los técnicos purgan el nitrógeno puro y lo rellenan con mezcla de gas. A partir de ahí, el gas fluye desde las líneas de suministro, a través de un filtro en el mezclador, hacia el sistema. Algunas configuraciones incluso usan un sistema de filtración secundaria corriente abajo del mezclador, pero antes de que el gas entre al espacio de trabajo del láser.
“Al tratar de mantener una pureza de gas Grado 5 [99.999%]”, dijo Bell, “puede aparecer contaminación en cualquier parte. Necesitan diseñarse sistemas completos que sean seguros en cuanto a la pureza del gas”.
Mezcla de gas para todo
Durante los últimos diez años, la mezcla de gas ha crecido de ser un proceso de nicho, principalmente usado para cortar aluminio, hasta convertirse en un método de corte de facto para acero al carbón grueso. Algunos podrían seguir usando nitrógeno solo por la brillantez, para lograr un borde brilloso, pero aquí también el gas mezclado se vuelto una alternativa viable.
“En los últimos dos o tres años”, hemos visto que casi cualquier material puede cortarse ahora con gas mezclado”, dijo Bell. “Esto depende de qué láser y qué potencia se tenga, y qué mezcla de gas se use para lograr los mejores resultados”.
El gas mezclado no es la panacea, pero ha abierto la puerta para algunas posibilidades de corte asombrosas. Conforme aumentan las potencias del láser de fibra, las mezclas de gas auxiliar están abriendo camino, de manera figurada y literal, para un corte rápido a alta velocidad en placa gruesa, que con frecuencia no requiere desbarbado secundario.
About the Author
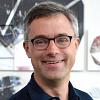
Tim Heston
2135 Point Blvd
Elgin, IL 60123
815-381-1314
Tim Heston, The Fabricator's senior editor, has covered the metal fabrication industry since 1998, starting his career at the American Welding Society's Welding Journal. Since then he has covered the full range of metal fabrication processes, from stamping, bending, and cutting to grinding and polishing. He joined The Fabricator's staff in October 2007.
About the Publication
Compañías Relacionadas
subscribe now
FMA Communications ha introducido al mercado la edición en Español de la revista The Fabricator. Esta versión consiste del mismo tipo de artículos técnicos y sección de lanzamientos de nuevos productos que actualmente presentan el personal de primera categoría de Fabricator en Inglés.
start your free subscription- Podcasting
- Podcast:
- The Fabricator Podcast
- Published:
- 04/16/2024
- Running Time:
- 63:29
In this episode of The Fabricator Podcast, Caleb Chamberlain, co-founder and CEO of OSH Cut, discusses his company’s...
- Trending Articles
Los operadores de prensa dobladora inexpertos hacen indispensable el repensar la seguridad
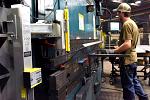
La mezcla de gas auxiliar impulsa la tecnología del láser de fibra
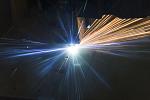
Prescripción para la reducción del desperdicio: arreglo esbelto de las instalaciones
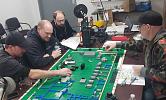
Máquina de corte por láser diseñada para el mercado mexicano
La sierra de doble carro sigue los contornos del tubo perfectamente
- Industry Events
16th Annual Safety Conference
- April 30 - May 1, 2024
- Elgin,
Pipe and Tube Conference
- May 21 - 22, 2024
- Omaha, NE
World-Class Roll Forming Workshop
- June 5 - 6, 2024
- Louisville, KY
Advanced Laser Application Workshop
- June 25 - 27, 2024
- Novi, MI