Editor
- FMA
- The Fabricator
- FABTECH
- Canadian Metalworking
Categories
- Additive Manufacturing
- Aluminum Welding
- Arc Welding
- Assembly and Joining
- Automation and Robotics
- Bending and Forming
- Consumables
- Cutting and Weld Prep
- Electric Vehicles
- En Español
- Finishing
- Hydroforming
- Laser Cutting
- Laser Welding
- Machining
- Manufacturing Software
- Materials Handling
- Metals/Materials
- Oxyfuel Cutting
- Plasma Cutting
- Power Tools
- Punching and Other Holemaking
- Roll Forming
- Safety
- Sawing
- Shearing
- Shop Management
- Testing and Measuring
- Tube and Pipe Fabrication
- Tube and Pipe Production
- Waterjet Cutting
Industry Directory
Webcasts
Podcasts
FAB 40
Advertise
Subscribe
Account Login
Search
Advanced fabricating technology moves Cadrex Monterrey forward
Machinery and lean manufacturing practices on full display in Mexico
- By Rafael Guerrero
- Updated April 9, 2024
- April 9, 2024
- Article
- Shop Management
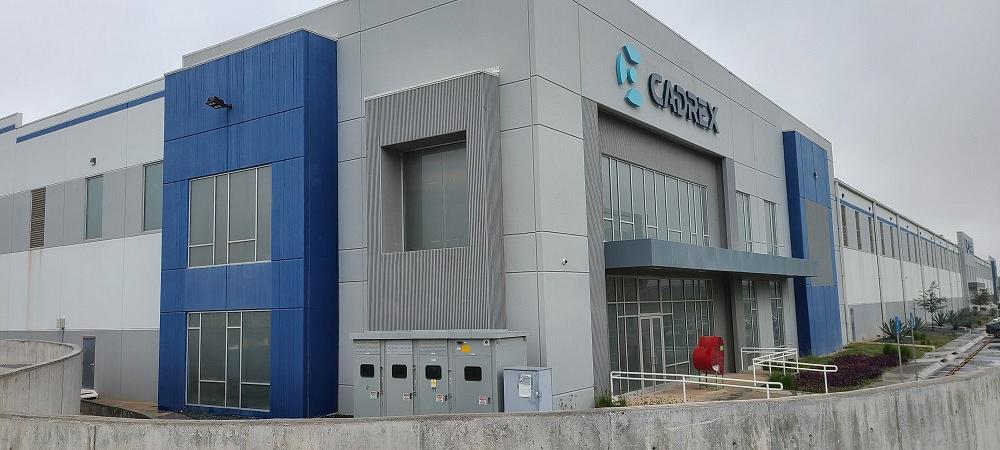
Cadrex has 21 facilities in North America, including one in Monterrey, pictured, the manufacturing hub of Mexico. It is one of the fabricator’s largest facilities, employing roughly 800 people.
From the outside, this Cadrex Manufacturing Solutions facility looks like any other building you’d find in an industrial park. You could even argue that its interior is typical too.
However, this 255,000-sq.-ft. facility is home to some of the most advanced metal fabricating technology in Mexico. It’s also the largest operation and one of the more important facilities belonging to the North American metal fabricating giant.
“The people running that industrial park said they had planned to fill it over the next eight years. The entire park filled up in eight months. The amount of manufacturing moving back to North America is driving that,” said Brian Steel, former Tenere CEO and current Cadrex CEO, in a conversation with The Fabricator in 2022.
When Cadrex, ranked No. 2 on the 2023 FAB 40 list, acquired Tenere Inc. in July 2022, the acquisition included the operations in Monterrey. It is a site with sheet metal fabrication, sheet metal stamping, welding, and plastic injection molding capabilities, serving clients in the data center infrastructure, network, computer, storage, fiber optics, 5G, and semiconductor markets.
“We like to be partnering with those companies that are high tech, that are in the game, that are in that top-notch market,” said Cadrex Monterrey Operations and Strategic Initiatives Vice President Federico Diaque.
“We have other segments for sure, but we want to be there, to be part of those companies that are heavily investing in innovation,” he added. “It's important for us to be in that niche.”
Like other businesses, Cadrex saw the potential in Monterrey. Its proximity to the U.S. provides a closeness to its American customers that wouldn’t be possible with an overseas facility. In a post-pandemic era of disruptions and delays, companies have been rethinking their supply chains for several reasons. As a result, nearshoring and reshoring continue to fuel the manufacturing growth of Monterrey.
Cadrex Monterrey can be considered a microcosm of Monterrey and manufacturing as a whole. It has found a way to innovate, evolve, and grow to cater to current and future customers’ needs—which in Cadrex’s case involves embracing things like lean manufacturing, automation, positive work environment, and going beyond sheet metal fabrication.
A Short Walk
Cadrex Monterrey’s shop was large, but given the fabricator’s plans, it wasn’t large enough. So in 2022, work began on a roughly 75,000-sq.-ft. addition. A walk through the production floor today immediately reveals the location of the addition—a wall separates the original part of the plant from the new section.
This addition allowed Cadrex Monterrey to reconfigure its product flow through a change in layout in 2023 and implement lean manufacturing processes.
The two new ACIES laser/punch combination machines have material handling and tooling changeout automation that speeds up part production when compared to parts made on stand-alone machines that require operator interaction for material loading and tooling changeover.
“When you walk the floor, you’ll be able to see the old way of doing things and then the new way of doing things,” Diaque said.
The new section allows a part to go from blanking to forming in the press brakes to assembly to shipping in less than 100 m across the width of the facility. In the other section of the facility, the start-to-finish distance is roughly 2,000 m, with parts having to travel a circuitous path to visit all the necessary value-added stops before shipping. This lean implementation has resulted in a quicker, less disruptive product flow that is more productive in a smaller space.
“It's all about people embracing the lean culture,” Diaque said.
“The worst thing we can have is ... sit back and relax and wait for someone else to pass us. We have to challenge ourselves,” he added.
This product flow won’t work for every part, though. It all depends on the volume and complexity of the product. Diaque said if complex parts require more assembly time than might be required for more simple fabricating, for example, then they are produced in the original part of the facility, where more area is available.
“Some customers we’re seeing today, they have over 500 different part numbers. The mix is much larger and you cannot” pursue the new route, Diaque said. “If you want to do it all in the same system, you kill flexibility—that's what we want to prevent as well.”
Not Sacrificing Quality
The first things you might notice in the Monterrey facility’s addition are the AMADA ACIES series punch/laser combination machines, complete with material storage towers and automatic tooling changers. They were among the facility’s newest machine additions in 2023 and join several other AMADA machine tools in the facility.
Diaque said the punch/laser combo helps Cadrex increase output without sacrificing quality. Operators aren’t needed to load sheets, so human interaction is kept to a minimum, helping prevent possible surface marring during handling. Tooling changeovers are done in seconds thanks to the automated tool change capabilities, a key addition to the company’s overall throughput.
“It allows us from a product standpoint to move forward, do much more faster changeovers, and make easier decisions when it comes to the operations,” Diaque said.
The new punch/laser combination machines also have helped Cadrex Monterrey to avoid major downtime associated with manually setting up tooling for complex jobs. The machines fabricate parts efficiently, giving Cadrex Monterrey consistent, repeatable results on these complex fabrications.
Sheet metal blanks from the laser/punch combination machines flow through Cadrex Monterrey’s bending department and then to assembly. This arrangement promotes a more efficient flow of parts.
Diaque added: “You have to be faster in doing your changeovers, which brings a challenge to your engineering team. But that’s part of being leaner and thinking, ‘How do we keep running and running?’ That allows you to respond quicker to customers.
“Customers will always come with urgencies: ‘I have an order that came out of the blue and it needs to be fulfilled right away.’ We can easily respond to those needs.”
Beyond Fabrication
On the other end of the facility, Cadrex Monterrey installed three new 300-ton sheet metal stamping presses in 2022 that make up part of its automated stamping line. It then purchased three new electric plastic injection molding presses in 2023 and situated them near the stamping presses. The company has had decades of experience in injection molding, and the Monterrey facility is that rare place in the metal fabricating world that has plastic part production capabilities as well as metal fabricating service offerings.
Diaque said the Mexico facility has four times the amount of equipment it did seven years ago. In a way, this rapid investment in capital equipment mirrors the investment manufacturers made in Monterrey overall.
“It's pretty unique. Usually when you have a metal stamping business, you won't see plastic equipment,” he said. “But we want to offer the vertical integration solution and other services to our customers.”
Automation is a key component of the Monterrey facility’s future. Diaque said there is room for automation growth in material movement, supplying material to the production floor, incorporating assembly solutions, and putting hardware into products.
Embracing Monterrey
In the last year, Cadrex Monterrey’s revenue has doubled, and it plans to grow revenue by another 30% to 50%. With roughly 800 employees, it is one of Cadrex’s largest and arguably most important facilities.
Cadrex Monterrey aims to take on smaller and lighter fabrication projects, Diaque said. It is a necessity given the shop’s involvement in parts production for data centers, a sector that is constantly changing as the demand for more real-time data and information grows. “The reason why [consumers] can use faster internet connections, better internet, and better communications is because all these products go into the data centers, into routers, all different shelves in those centers,” he said. “Without it, we might not be seeing what we’re seeing today.”
The facility employs a mix of blue- and white-collar workers, and at least 75% of its workforce is on the shop floor. Diaque said almost 40% of them have been with the company since before the acquisition.
Company officials aren’t worried about attracting additional employees should the Monterrey facility continue to take on more work. The Cadrex facility is in close proximity to a talented labor market and some of the best universities in the country.
Cadrex Monterrey leaders believe in on-the-job training to expand the skills of its employees. Its training department has created on-the-job certifications aligned with machine operation and basic maintenance. It also provides specific training courses for skills such as welding.
Employees have opportunities for advancement should they want it. Diaque said his goal is to fill the majority of the company’s new positions with internal candidates.
“You want to have people that embrace the company, that feel a part of the company. You need to see the opportunity there,” Diaque said.
Cadrex’s acquisition of Tenere is one of several in the last few years that has helped the fabricator grow to 21 facilities, 600-plus machines, and 1.5 million sq. ft. of space. Diaque said Monterrey is constantly working with other Cadrex facilities. Monthly reviews keep leaders of each site engaged in what’s happening elsewhere, what’s working and what isn’t working. The implementation of Microsoft Power BI software allows for the sharing of production, planning, productivity, and safety data.
“It has been evolving during 2023, with all these companies being acquired. It takes time,” he said.
And it is possible the Monterrey site is not done growing.
“Don't be surprised if in a year from now you see another 100,000-sq.-ft. space or so,” Diaque said.
About the Author
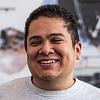
Rafael Guerrero
2135 Point Blvd.
Elgin, IL 60123
(815)-227-8242
Rafael Guerrero. was named editor of The Welder in April 2022. He spent nine years as a journalist in newspapers in the Midwest and Pacific Northwest, covering topics and communities in central Illinois, Washington, and the Chicago area.
Related Companies
subscribe now
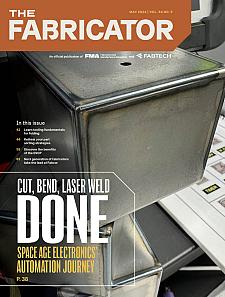
The Fabricator is North America's leading magazine for the metal forming and fabricating industry. The magazine delivers the news, technical articles, and case histories that enable fabricators to do their jobs more efficiently. The Fabricator has served the industry since 1970.
start your free subscription- Stay connected from anywhere
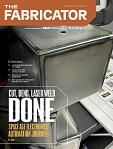
Easily access valuable industry resources now with full access to the digital edition of The Fabricator.
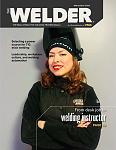
Easily access valuable industry resources now with full access to the digital edition of The Welder.
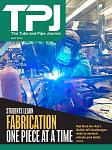
Easily access valuable industry resources now with full access to the digital edition of The Tube and Pipe Journal.
- Podcasting
- Podcast:
- The Fabricator Podcast
- Published:
- 04/16/2024
- Running Time:
- 63:29
In this episode of The Fabricator Podcast, Caleb Chamberlain, co-founder and CEO of OSH Cut, discusses his company’s...
- Trending Articles
Tips for creating sheet metal tubes with perforations
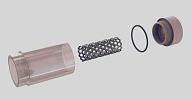
Supporting the metal fabricating industry through FMA
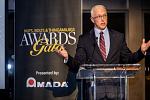
JM Steel triples capacity for solar energy projects at Pennsylvania facility
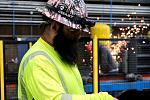
Fabricating favorite childhood memories
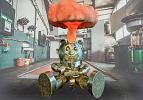
Omco Solar opens second Alabama manufacturing facility
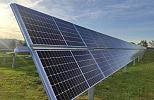
- Industry Events
16th Annual Safety Conference
- April 30 - May 1, 2024
- Elgin,
Pipe and Tube Conference
- May 21 - 22, 2024
- Omaha, NE
World-Class Roll Forming Workshop
- June 5 - 6, 2024
- Louisville, KY
Advanced Laser Application Workshop
- June 25 - 27, 2024
- Novi, MI